Toyota was once a leader in electrification, thanks to its hybrids, but the transition to electric vehicles has been more challenging for it. After tearing down and reverse engineering a Tesla Model Y, its engineers are now starting to understand why.
“Taking the skin off the Model Y, it was truly a work of art,” an engineer who participated in the teardown told Automotive News. “It’s unbelievable.”
Although Toyota is famed for its engineering and manufacturing acumen, its engineers realized that Tesla has a “whole different manufacturing philosophy,” and that it needs a “new platform designed as a blank-sheet EV,” two executives said.
That’s because, despite looking relatively unchanged on the outside, the latest generation Model Y has improved immensely under the skin. The use of “giga casting” has eliminated many parts while the batteries are allowed to act as a structural floor, two factors that have helped the EV company simplify and improve its vehicles.
Read: Tesla Is Using Its Big Profits To Cut Costs And Undercut The Competition
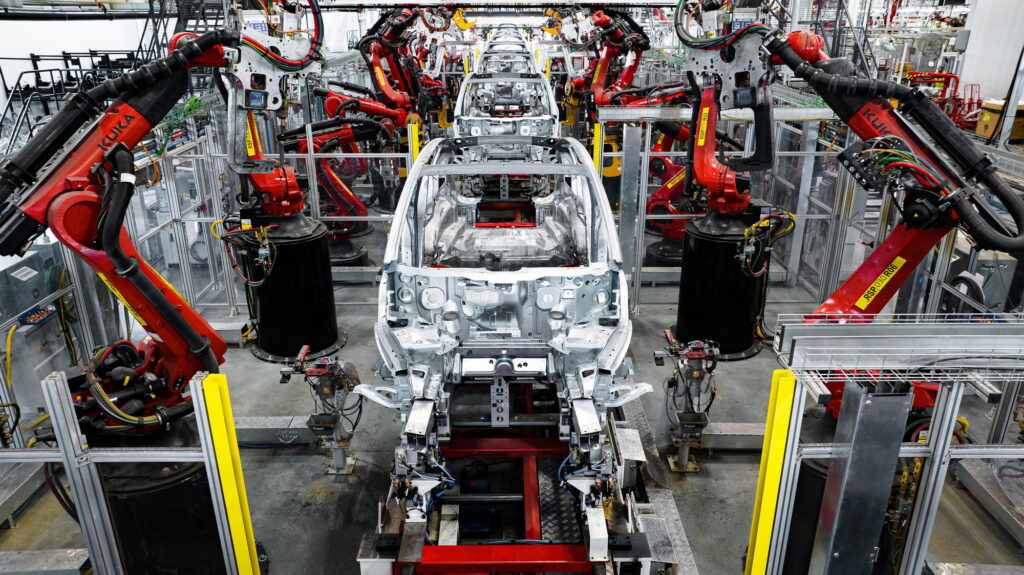
Its foundation as an electric-only automaker, too, has led to some advantages. Whereas legacy companies are likely to repurpose parts, such as cooling hoses, from their internal combustion vehicles, Tesla realized that it could use slimmer hoses made out of cheaper materials, because the cooling needs of EVs are lower.
By one estimate, the cooling hoses alone save 11 lbs (5 kg) and $25 per car. Overall, Tesla is able to save up to 220 lbs (100 kg) per vehicle. That not only makes the vehicles lighter and cheaper to produce, it also helps improve their range.
For its first batch of modern EVs, meanwhile, Toyota turned to its TNGA platform. Although it was innovative when it was first introduced, it serves as the foundation of both its electric and internal combustion vehicles.
Unfortunately for Toyota, the electric vehicles based on it haven’t impressed. The bZ4X has been dogged by issues and has underperformed in the real world. And it can’t simply add more batteries, because its axles and side beams can’t accommodate them.
Read: ‘Disappointing’ 134-Mile BZX4 Achieves Half The Advertised Range In Danish Test, Toyota Investigating
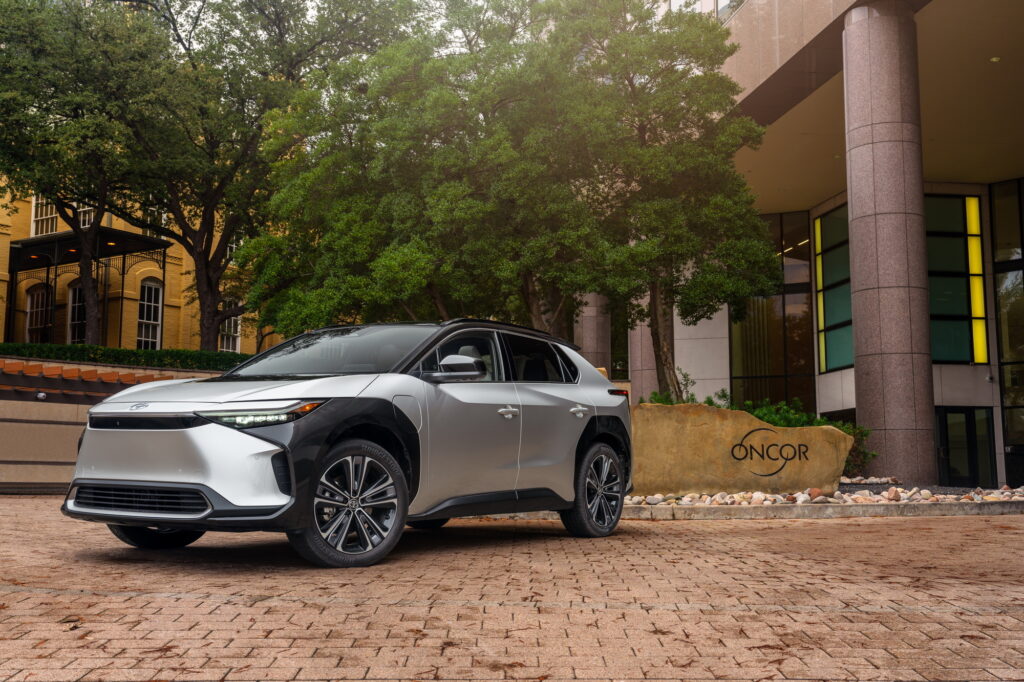
While the Tesla teardown has given Toyota more perspective on its EV issues, it has long known that it’s falling behind. Before he stepped down in January, former Toyota CEO Akio Toyoda had asked the company’s engineers to pitch their next-gen EV solutions.
The company also delayed the release of new bZ models and reshuffled the EV team. It assigned R&D legend Shigeki Terashi to the EV team, as well as Takero Kato, the top Toyota engineer at its joint venture with BYD.
The Chinese company is one of the world’s top-selling EV manufacturers and has already helped Toyota cut down on development times for EVs. It can’t solve all of the automaker’s problems, though.
For one thing, Toyota has higher reliability standards than BYD. For another, expectations of EVs are different in China than they are in the U.S., for instance. Moreover, Toyota is still in the midst of the expensive process of retrofitting factories for its TNGA platform.
“Can we change our manufacturing situation, which is a kind of hindrance to the future?” an executive asked. “We have to plan for the next 20 years, not just the next five, and make sure that the right vehicles are in the right place and the right time.”
To be sure, Toyota can’t abandon the bZ model range immediately, since it has to meet emissions requirements in Europe. But the company is facing some difficult questions if it wants to remain competitive in the EV game.
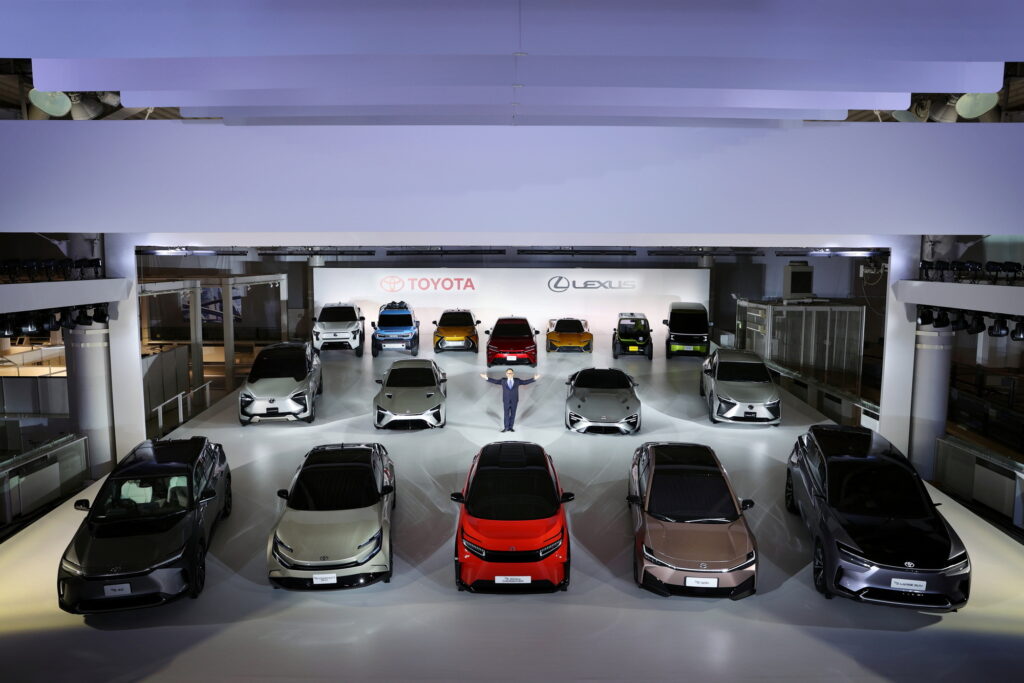