The latest version of Toyota’s luxurious Century is currently under production at its Tahara Plant in Japan. This new SUV, the first to wear the Century nameplate, is meticulously handcrafted by a dedicated team of 40 skilled workers, hand-picked from a pool of 1,500 employees. To secure their place on the assembly line, these workers had to successfully complete a rigorous three-part exam.
Hiroki Tanaka, one of the workers who was selected for the team, had to undergo a mandatory course and successfully pass a certification exam to secure a place on the team. The exam comprised three modules: an initial assessment of basic skills, a written test covering the Century’s history, vehicle structure, and related topics, and a practical examination to showcase proficiency in building the luxury series.
“The written exam was more difficult than the practical, with 200 questions, but I got through it by hitting the books hard for the first time since my student days,” told the Toyota Times. “I learned many new things, from the history of Toyota and the Century to the car’s unique high-quality fabrication techniques. It was an invaluable experience.”
Read: Toyota Century SUV Debuts As The Pinnacle Of Japanese Opulence
Gaining experience from the Land Cruiser line
The 35-year-old assembly worker has been employed by Toyota since 2007. A graduate of its Technical Skills Academy, he says that he was thrilled to immediately start working on the Land Cruiser line because it was his dream car, and the work soon provided him with the opportunity to buy one of his own.
His experience assembling Land Cruiser chassis set him up well for his current work, which sees him attaching suspension components to the Century. His work is particularly important, because any errors are felt in the rest of the vehicle.
Precision is always a focus of attention for Toyota, but in the luxurious Century, it’s an obsession. Whereas the automaker allows for 20 percent torque deviation from spec in its typical vehicles, it allows just 5 percent deviation in the premium SUV.
“On any assembly line other than the Century, each nut or bolt is tightened in a single pass with a fastening tool,” said Tanaka. “On the Century assembly line, however, the stringent precision requirements mean that we first use a jig to tighten by hand, then tighten again with a fastening tool to get closer to the target torque. Lastly, we use a digital torque wrench, whose torque values are uploaded to the computers, working by hand to obtain the final value.”
Getting it right is harder than it sounds, Tanaka says. That’s especially true under the vehicle, where torque ratings tend to be higher. He says that on any part that requires more than around 150 Nm (110 lb-ft) of torque, he has to put his whole body into tightening, making precision adjustments difficult.
That means that he can spend up to a minute tightening larger parts, which is 12 times longer than the five seconds it takes workers to tighten nuts and bolts on other vehicles. That means that Toyota produces just three examples of the Century per day.
Four production sections
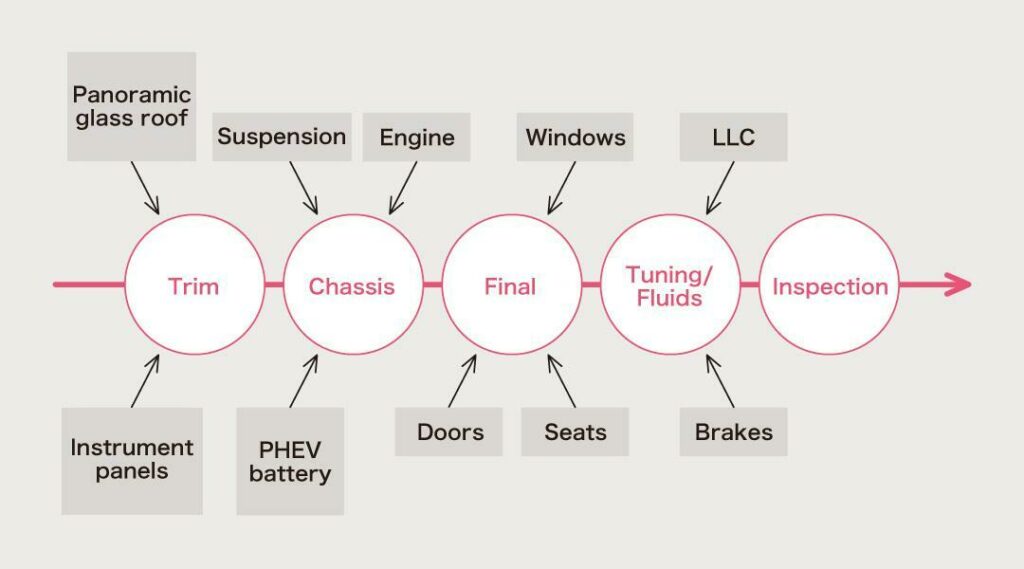
On the Century assembly line, these handpicked workers are divided into one of four specialized sections: Trim, responsible for managing components like instrument panels and roofs; Chassis, in charge of engine installation, suspension, and PHEV battery integration; Final assembly, dealing with seats, doors, and windows; and Tuning/Fluids, overseeing tasks such as engine coolant and brake systems.
The result is a beautifully finished SUV, and shows that despite all the automation in modern car factories, craftspeople are still central to making the best vehicles.