- Bentley is installing a high-tech driving sim at its factory to test ride comfort, cabin acoustics, and more.
- The sim will speed up development by reducing the automaker’s dependence on real-world testing in far-flung locations.
- In so doing, it will help cut around 85 tons of CO2 emissions per prototype.
Modern cars require a ton of testing and, before they go into production, most vehicles spend hundreds of days testing in the real world — incidentally, that’s why we get to see spy photos of upcoming vehicles before automakers are ready to show them off. But Bentley wants to make vehicle testing greener and faster (and make our photographers’ lives harder) by doing more of it virtually.
The automaker will install what it refers to as a Compact Full Spectrum Driving Simulator at its Dream Factory in Crewe. Essentially, it’s a really fancy driving simulator that Bentley will use to test the comfort of its upcoming vehicles.
Read: VW’s Innovation Hub Is Working On Wireless EV Chargers And Other Game Changing Tech
“The introduction of the first, all-encompassing ride frequency driving simulator at Bentley is a key moment for us,” said Charlie Smith, Virtual Vehicle Engineering at Bentley. “This state-of-the-art system represents a significant advancement in our virtual development capabilities and will allow us to refine core Bentley attributes in a dynamic, driver-in-the-loop virtual environment for the first time.”
The rig will be able to simulate a variety of road surfaces, including potholes and bumps, and will allow engineers to assess ride comfort, cabin acoustics, and vibrations before a new prototype hits the road.
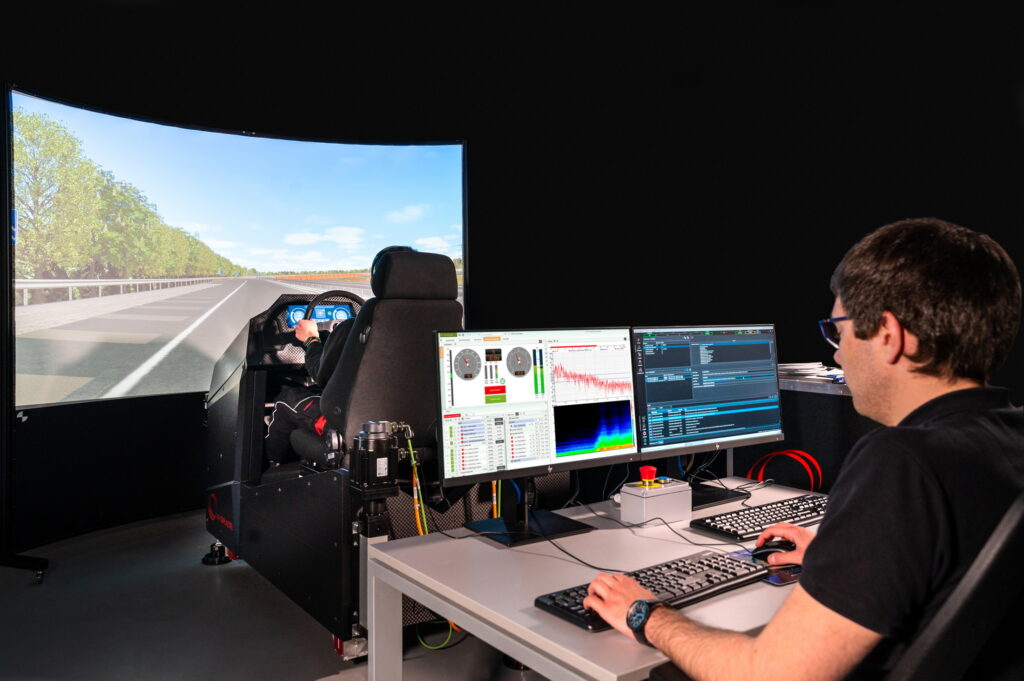
“It offers unprecedented precision, ensuring that every Bentley delivers the unparalleled luxury and performance our customers demand,” said Smith. “This simulator is a strategic step towards accelerating our product development cycle, minimizing reliance on physical prototypes and enhancing simulation capabilities.”
The simulator was developed in Italy by VI-grade, and in addition to speeding up development of new vehicles, it will also help the automaker lower its emissions. By allowing Bentley to run around 350 fewer days of road testing, it will save around 85 tons of CO2 per vehicle prototype.
“Beyond its technical capabilities, the Dynamic Driving Simulator brings substantial sustainability benefits, reducing the need for both physical prototypes and extensive physical tests, the latter often involving cars and colleagues shipped to remote locations around the world,” said Dr. Matthias Rabe, Bentley’s head of engineering. “As our customers would expect, the system will also play a key part in defining the luxury experience associated with every Bentley car.”