Volkswagen is bringing more of the EV manufacturing and development process in-house. The automaker announced the decision at its Tech Day 2023, promising that making its own batteries, electric motors, pulse inverters, and thermal management system from the ground up will make them work together more efficiently, and more cost-effectively.
“Our goal is to achieve technological leadership, also in electric mobility,” said Thomas Schmall, Volkswagen’s head of technology. “In future, this will make the Volkswagen Group one of the only car manufacturers in the world that’s able to offer a holistically optimized complete system.”
The brand already makes its own batteries and motors, but today announced that it will make its own pulse inverters and thermal management systems. The former, the automaker says, is the brain of the electric drivetrain.
Read: VW Won’t Cut EV Prices To Match Tesla, CEO Says
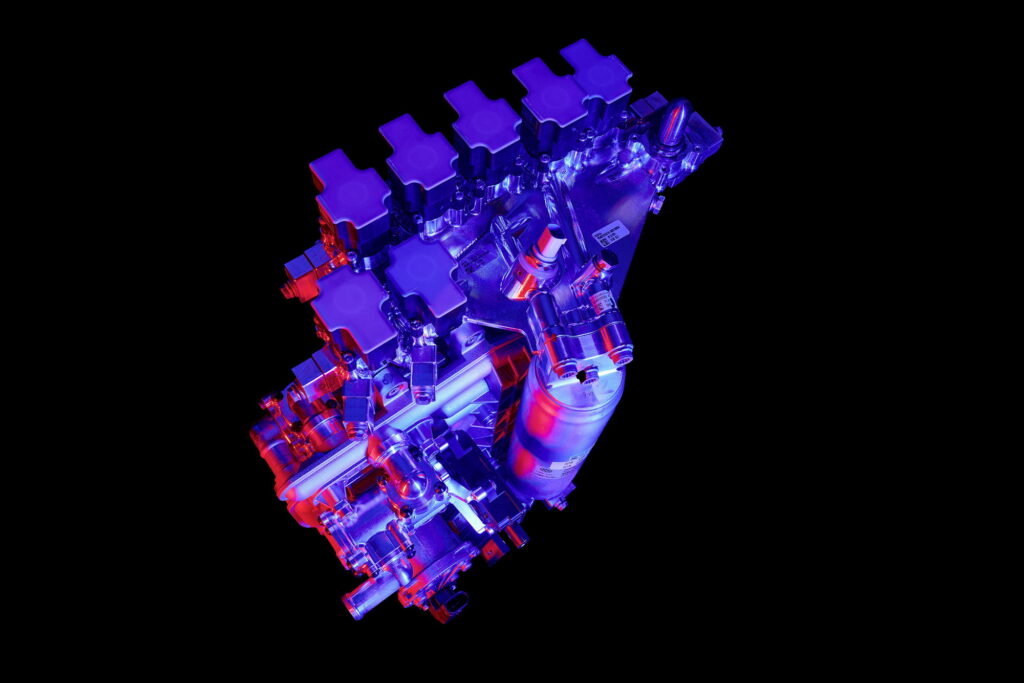
Responsible for the efficiency and performance of the powertrain, the pulse inverter is a very important part. Volkswagen’s developers, therefore, have redesigned it from the ground up for the MEB platform, in this generation and the next.
671 HP And Beyond
As a result of VW’s modularity, it will be possible to fit the same pulse inverter into everything the Volkswagen Group makes. That means that everything from the lowest-powered city car to sports cars with outputs of over 671 hp (500 kW/680 PS), the automaker says.
The thermal management system, meanwhile, will replace present day systems—which are saddled with lots of hosing and individual components—with an extremely compact module that controls both the cabin temperature, and the battery’s temperature.
Improving the thermal management system will have a major impact on driving range and how quickly it can charge. The new unit will also be lighter, and more efficient than the systems used in VW EVs today.
In all, Volkswagen believes that by designing these systems to work specifically for its own batteries and motors, it can achieve 20 percent more efficiency from its vehicles. From a manufacturing standpoint, meanwhile, the automaker will be able to generate economies of scale by standardizing these parts across its many brands, including Audi, Porsche, Skoda, and even partners like Ford and Mahindra.
The thermal management system and the pulse inverter will work alongside VW’s upcoming unified battery cell, which will be used in vehicles as of 2025.
“The Volkswagen Group and its brands stand for first-class products and technologies,” said Oliver Blume, chair of VW Group board of management. “Thanks to the size and breadth of the Group, as well as our in-house expertise, we can leverage enormous economies of scale. This benefits our customers and makes our vehicles even better.”
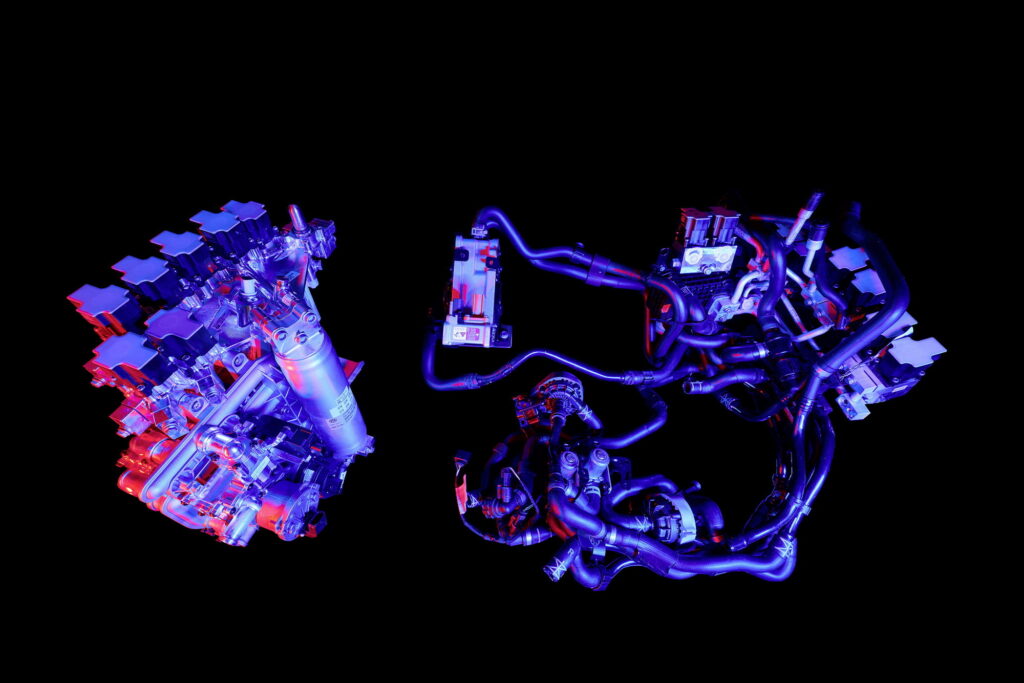