Zeekr has revealed that it is using the ‘gigapress’ die-casting technique first implemented by Tesla to cut production costs of the all-electric 009 MPV.
In the case of the 009, the Chinese car manufacturer is using big aluminum die casts to make a large rear underbody section of the vehicle, measuring 1.4 meters long and 1.6 meters wide. This alone has allowed it to reduce the number of welding points by almost 800. Furthermore, it makes the vehicle lighter, increases the structural stiffness, and should reduce defects, Zeekr manufacturing technology chief Jiang Kehong revealed.
Read: Zeekr 009 Is An Electric Luxury Minivan With 536 HP And 511 Miles Of Range
Tesla started using aluminum die-casting machines for the Model Y in late 2020. The machine it uses are manufactured by Italy’s Idra Group and use shots of molten aluminum that are injected into a cold-chamber casting mold. Once the piece has solidified, it is removed and robots clean the chamber for the next cast. Tesla’s Giga Press can produce up to 45 castings per hour.
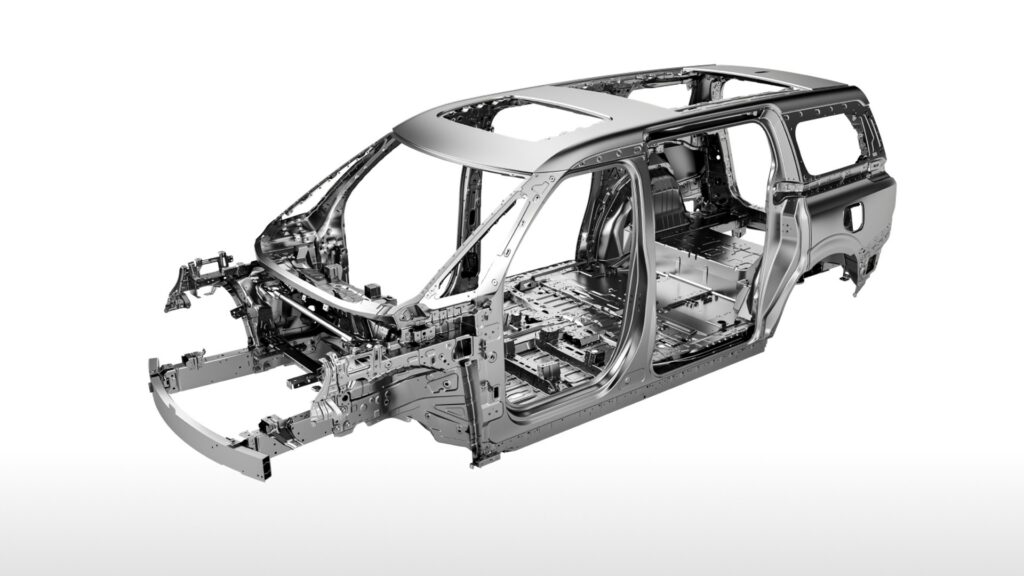
Speaking with Reuters, Jiang noted that Zeekr will use giga-casting technologies on more of its models “in the future.”
Zeekr began investigating the possible use of die casting in 2020 and sources its presses from Chinese company LK. These machines have a pressing power of 7,200 tons and Zeekr’s use of the technology comes shortly after rival Nio introduced its new chassis designed to slash manufacturing costs.
There is a drawback to manufacturing large pieces, however. As large body sections are made from a single piece, any damage that a part may suffer in a crash could necessitate the expensive replacement of an entire section of the vehicle. Zeekr says it has addressed this by developing a system that allows it to change select parts of the large die-cast section without having to replace the entire panel.
“That should help reduce the repair cost after an accident,” Jiang noted. “We believe customers should not pay extra for our technology innovation.”
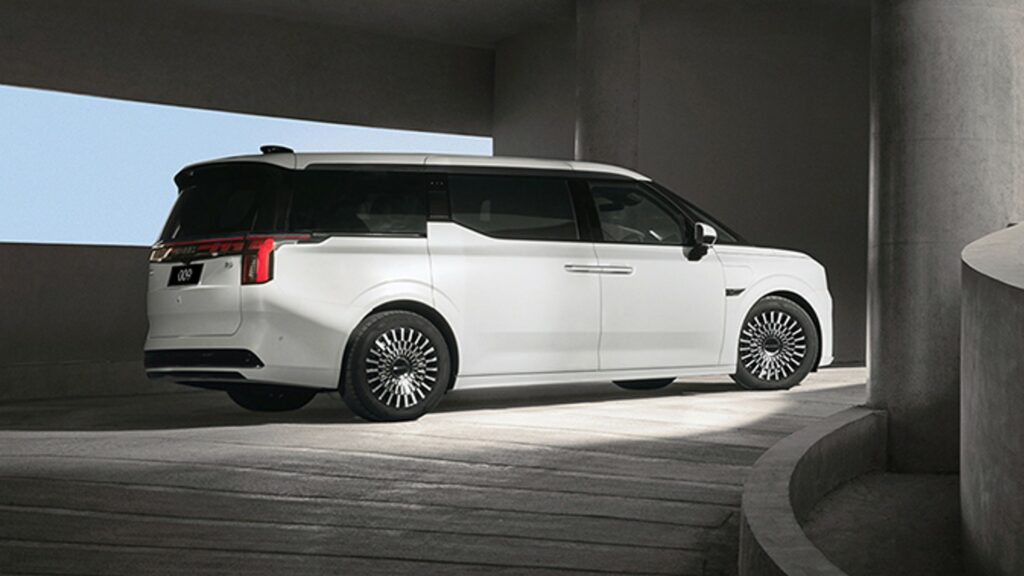